BeAM and PFW Aerospace are glad to announce their partnership to qualify an aerospace component for a large civil passenger aircraft using Ti6Al4V which fulfils typical aerospace quality requirements. In addition, this collaboration focuses on industrialising the DED process to manufacture series components.
In the midst of the fourth industrial revolution and its associated digitalisation of industrial manufacturing, additive manufacturing is becoming a significant future-oriented alternative to conventional manufacturing methods. Additive manufacturing processes for certain applications have clear benefits, above all in the aerospace industry, in which component weight, low production volumes and small batch numbers play a significant role.
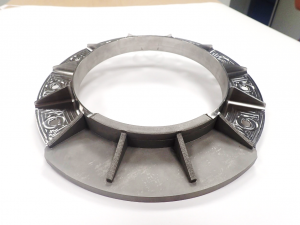
Aerospace flange in Ti6Al4V
Built using DED, heat treated and partially machined
PFW has been scanning technological developments and the market for additive manufacturing processes for four years. It is an international tier one supplier of systems and components for all civilian Airbus models as well as the Boeing 787 Dreamliner. PFW has the ability to establish designs for AM and to perform qualifications. This is due to its status as a build-to-spec developer, and with its experience in qualifying components and processes.
In particular, materials which are expensive to process such as titanium alloys are predestined for AM. PFW is working closely with BeAM, a Strasbourg, France company, on Directed Energy Deposition (DED) in order to test the applicability of this process to currently machined titanium components and complex welding designs.
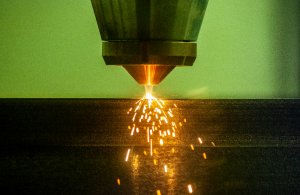
DED is an Additive Manufacturing process where focused thermal energy is used to fuse materials by melting them as they are deposited.
DED can give complex characteristics to semi-finished products or intermediate construction. The results are near-net-shape geometries in which completing production is only a simple programme for finishing the surface. This can reduce material expense as well as scrap volume by over 70%, which has a sustainable effect on process cost effectiveness. PFW is striving to create a process combining cost-effective manufacturing of geometrically simple intermediate products and jobs with complex, additive characteristics.
BeAM is the only system manufacturer in Europe which can provide systems for high-quality processing of titanium on a 5-axis system. PFW acquired a Modulo 400 machine whose glove box design makes it possible to fulfil aerospace requirements needed for overall atmospheric values for O2 and H2O. System technology and process management are being further developed in close cooperation to meet industrial production requirements.
About PFW Aerospace
PFW Aerospace GmbH has been one of the most important companies in German aviation for over 100 years. The company is seen as global leader in the field of tubing systems in aircraft. The entire range of services also includes structural components, such as belly fairings, pressure bulkheads, pressurised floors, support constructions, RAT frames, landing flaps, lighting covers, ram-air outlets, APU compartments and also fuel tanks. PFW Aerospace GmbH employs around 2,000 people at its locations in Speyer (Germany), Nuneaton (Great Britain) and Izmir (Turkey).
About BeAM
BeAM, created in December 2012, is a pioneer in designing and producing industrial metal additive manufacturing machines using the DED technology (Directed Energy Deposition). BeAM works closely with its customers and business partners to develop and industrialize manufacturing and repair processes with feasibility assessments, pilot production, sales of systems, training and technical support. BeAM has two Solution Centers, one in Cincinnati, Ohio and one in Singapore. This global presence of engineers trained by BeAM contributes to accelerating the adoption of its innovative technology, while offering engineering services for local industrial companies.
In June 2018, BeAM joined the AddUp Group, a manufacturer of 3D printing machines and production lines based in Clermont-Ferrand. AddUp is a joint-venture between Fives and Michelin, which employs more than 220 People.
Press Contact
PFW Aerospace – email hidden; JavaScript is required – Phone: +49 (0) 6232 616 – 0
BeAM – Frédéric Le Moullec – email hidden; JavaScript is required – Phone: +33 3 88 60 87 62